A well-known problem with the lysis operation is the real-time increase in viscosity when the NaOH-SDS buffer mixes with resuspended bacterial cells. This results in pumps needing to be adjusted during the process in real-time. Changes in viscosity are mainly observed in the alkaline step and are caused by degraded genomic DNA passing through narrow passages of static mixers. Viscosity have been shown to be as high as 150 mPas, or approximately the viscosity of olive oil (Ciccolini et al. 1999):
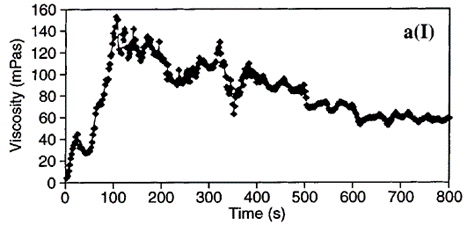
- The Alker 3L system implements flowrate feedback control which automates real-time pump adjustments to maintain the set lysis time. The controller is responsible for automatically balancing pump speeds by sampling real mass flow rates and projecting finishing times. The controller thus enables fully automated control of the entire process, continuous monitoring of the observed lysis time, and depletion of starting solutions at the same time.
- The controller can be tuned based on the desired level of process intervention. High degrees of process control follow the Process Analytical Technologies (PAT) advanced GMP manufacturing concept introduced by regulatory guidelines (e.g. ICH Q14). Critical process parameters such as the lysis time can be measured in 3.5 second intervals and corrective changes to pump rates can be made in real time. Process parameters are thus continuously altered to meet the varying viscosity demand. As a result, variation in process variables is considerably higher than in traditional manufacturing. The Alker 3L control software allows the flexible application of controller coefficients such that the controller can be turned off if a traditional manufacturing process mode is desired. The procedure for tuning controller PID parameters can be found in section: 5.5 PID controller tuning.
Leave a Reply